Diecasting in Malaysia has grown into a crucial sector within the country’s manufacturing industry, supplying high-quality metal components to various global markets. This advanced metal-forming process involves injecting molten metal into a mold cavity under high pressure to create precise and durable parts. Industries such as automotive, aerospace, electronics, and consumer goods heavily rely on die-cast components due to their strength, accuracy, and efficiency in mass production. Malaysia’s strategic location in Southeast Asia, combined with its skilled workforce and strong industrial infrastructure, has made it an attractive hub for Diecasting companies. With increasing investments in technology and automation, the Malaysian Diecasting industry continues to evolve, adapting to the growing demands for lightweight, high-performance components. As global manufacturing standards rise, Malaysian Diecasting companies are positioning themselves as key players in the competitive international market.
The materials used in Diecasting play a significant role in determining the final product’s properties, and Malaysian manufacturers specialize in working with aluminum, zinc, and magnesium alloys. Aluminum Diecasting is the most widely used due to its lightweight nature, corrosion resistance, and high thermal conductivity, making it ideal for automotive and aerospace applications. Zinc Diecasting is favored for its precision and impact resistance, often used in electronic housings, mechanical components, and decorative hardware. Magnesium Diecasting, though less common, is gaining traction for its exceptional strength-to-weight ratio, making it an attractive choice for industries focused on reducing material weight without compromising durability. As material science progresses, Malaysian Diecasting firms continue to refine their techniques, exploring new alloy compositions to enhance product performance and longevity.
One of the main advantages of Diecasting in Malaysia is the ability to produce complex, high-precision components with minimal post-processing. Unlike traditional manufacturing methods, Diecasting allows for the creation of intricate designs with tight tolerances, reducing the need for additional machining. This efficiency results in faster production cycles and cost savings, making Diecasting an economically viable solution for mass production. Malaysian manufacturers have embraced state-of-the-art machinery, automation, and computer-aided design (CAD) technologies to enhance precision and consistency. These advancements help maintain uniform quality across large production batches while reducing material waste. With growing global demand for precision-engineered components, Malaysia’s Diecasting sector is well-equipped to meet the challenges of modern industrial manufacturing.
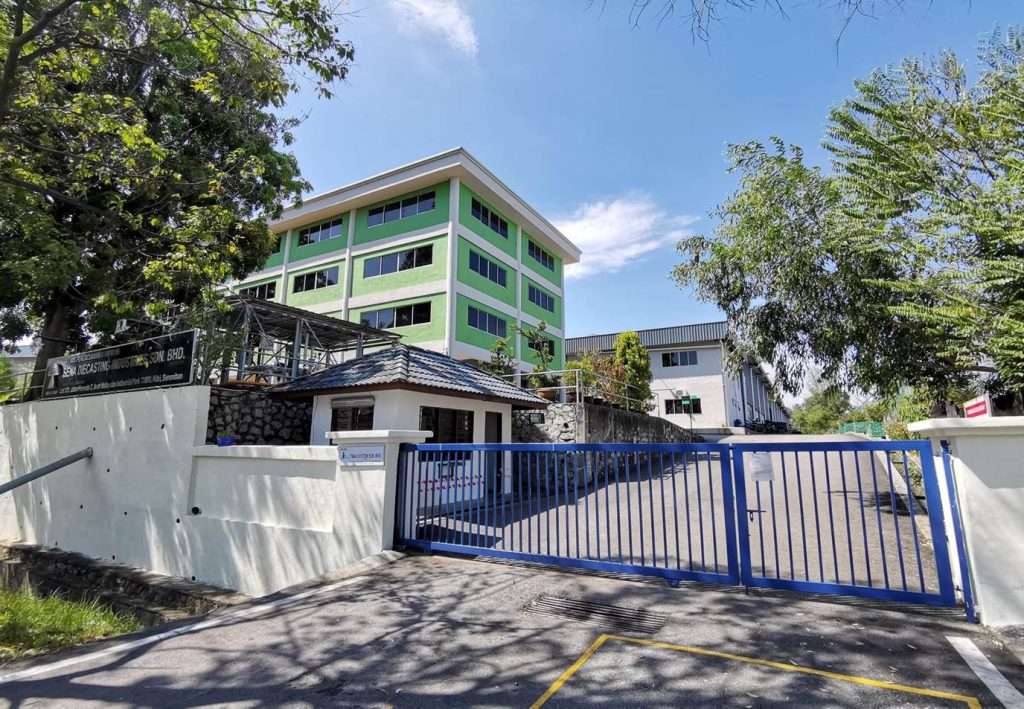
Sustainability is becoming a major focus for the Diecasting industry, and Malaysian manufacturers are actively adopting environmentally friendly practices. Many companies have implemented metal recycling programs to reduce raw material waste, ensuring that excess aluminum, zinc, and magnesium are repurposed for future production. Energy-efficient technologies, such as optimized casting techniques and automated cooling systems, have also been introduced to lower carbon emissions and improve overall resource efficiency. Additionally, advancements in vacuum-assisted and low-pressure powder coating malaysia techniques have contributed to reducing defects and increasing yield rates, further minimizing waste. The Malaysian government has set regulations to promote sustainable industrial practices, encouraging Diecasting companies to innovate in ways that align with global environmental standards. As the industry moves towards greener production methods, Malaysia is steadily becoming a leader in sustainable Diecasting manufacturing.
Government support and investment in the Malaysian Diecasting industry have played a crucial role in its expansion and modernization. Various initiatives, including tax incentives, funding for research and development, and infrastructure upgrades, have helped manufacturers enhance their capabilities. Industrial parks equipped with advanced facilities provide an ideal environment for Diecasting companies to scale their operations and collaborate with international clients. The government’s focus on Industry 4.0 initiatives, such as automation, data analytics, and smart manufacturing, has further strengthened the country’s competitive edge. Additionally, Malaysia’s involvement in free trade agreements and global supply chains has opened doors for local Diecasting firms to expand their exports. By fostering innovation and maintaining high-quality production standards, Malaysia continues to attract foreign investments and solidify its position as a key player in the global Diecasting market.
The future of Diecasting in Malaysia looks promising, with ongoing advancements in technology, materials, and sustainability practices shaping the industry. The demand for lightweight, high-strength components is expected to grow, particularly in the automotive and aerospace sectors, where efficiency and fuel economy are paramount. The integration of artificial intelligence, robotics, and real-time monitoring systems will further optimize production processes, ensuring higher precision and reduced waste. As manufacturers continue to embrace digital transformation and smart manufacturing, Malaysia’s Diecasting industry is set to achieve greater efficiency and global recognition. With a strong foundation built on innovation, government support, and a skilled workforce, Malaysia is poised to remain a leader in the Diecasting sector for years to come, driving excellence in precision manufacturing.